東京都ものづくり生産性革新スクール 事例紹介
CASE1 株式会社 今野製作所
「力をあわせる力がある。」を理念に、
技術部門と製造部門で連携プレー
「ムダ」な業務の洗い出しに成功し、生産性を大幅にアップ!!
技術部門と製造部門で連携プレー
「ムダ」な業務の洗い出しに成功し、生産性を大幅にアップ!!
株式会社今野製作所 |
|
![]() |
![]() |
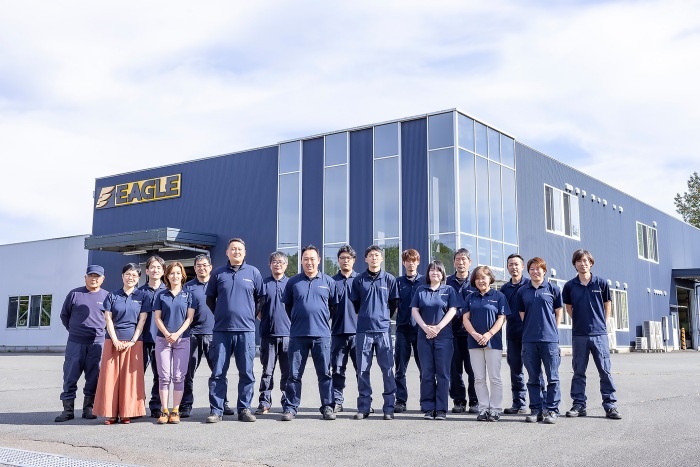
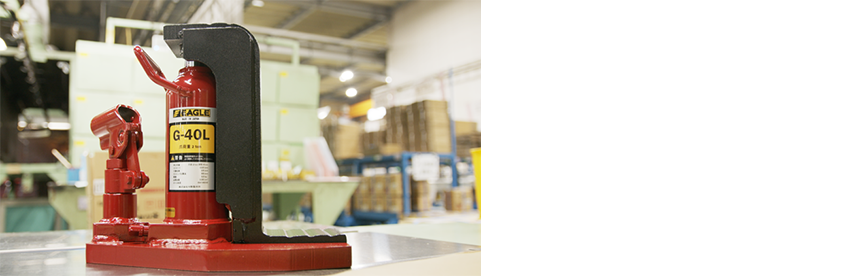
公社では、中小企業の持続的な成長において、新たな付加価値を生み出す「生産性の革新」を担う「中核人材」の育成を目的として、平成28年より「東京都ものづくり生産性革新スクール」(以下、スクール)を開講し、毎年実施している。
昨今、技術革新やデジタル技術の導入が飛躍的に進む一方で、急激な感染症拡大や不穏な世界情勢の影響等により中小企業を取り巻く環境は大きく変化しつつある。それに伴い、企業の中核人材育成の重要性がより一層高まっており、同スクールへ寄せられる期待も大きい。
本稿では、第1期生から同スクールに参加し、計4名のスクール修了生を輩出している今野製作所を紹介。なかでもスクールで学んだ内容をもとに、目に見える改善効果を出している同社福島工場に焦点を当て、スクールに参加した理由や、スクールで学んだ経験が現在、どのように生かされているのかを聞いた。
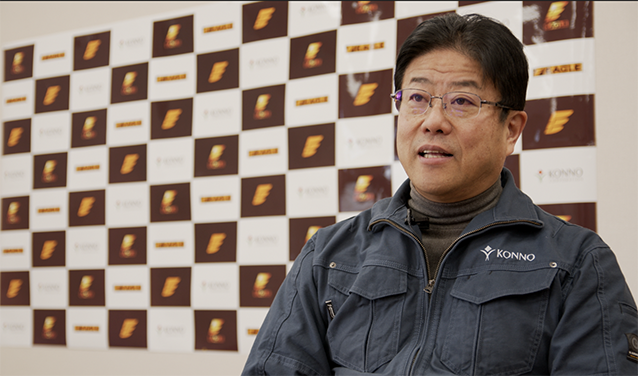
今野社長 当社ではスクール受講以前からも長い間、現場の改善活動に取り組んできました。しかし、始めた当初に比べ、次第に成果が出にくくなってきたと感じていたところ、スクール開講を知ったのです。そこで改めて学び直し、会社としてもう一段、レベルアップを図りたい、と思ったのがきっかけです。
——御社ではスクール開講当初から複数の社員を受講させ、現場改善をされています。なかでも福島工場の社員がスクールに参加し、現場改善を実践したことで大きな成果を上げていると聞きました。
そこで、折笠福島工場長をはじめ福島工場の現場改善に関わった社員の皆さんにいろいろとお話を伺いたいと思います。
まずは、折笠工場長にお聞きします。福島工場としてスクールの受講を希望した経緯について教えてください。
折笠さん 以前からスクールの話は社内でも耳にしていました。福島工場でも当時抱えていた問題の解決・改善を進めたいと考えていたため、目黒に参加してもらったのです。受講したのは目黒1人でしたが、学んだことを現場で実践する際には色々なメンバーを巻き込んで、課題ごとに担当を振り分けて取り組んだことで、社員全員が生産性向上を意識するようになったと感じています。
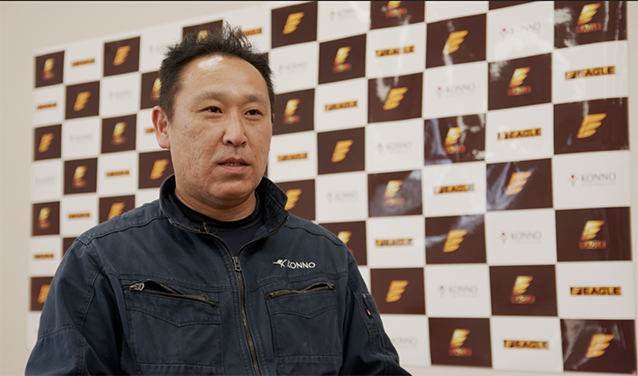
折笠さん これまでにも現場改善は行っていたのですが、前工程と後工程とでばらばらに取り組んでいたので、改善した部分だけ見れば生産性が上がっていても、改善していない部分は生産数が追いつかなくなるーー全体でみれば問題が解決できていない、という繰り返しで、根本的な解決ができずにいました。
が、目黒がスクールで学んだことを工場内で共有したことで、一人一人が日々問題点や生産性・会社の利益などに目を向けるようになり、今では社員全員が同じ方向を向いているチームに成長できたと感じています。会社全体で改善に取組む意識を持つことで、全員で工程におけるボトルネックを見つけ出し、改善していくスピードが格段に上がったと思います。
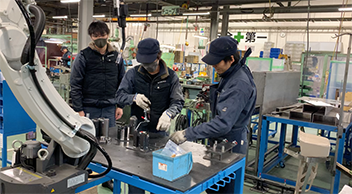
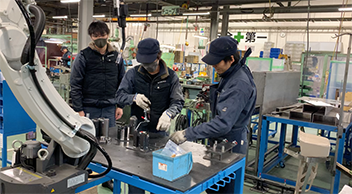
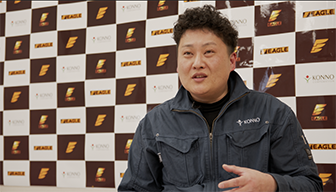
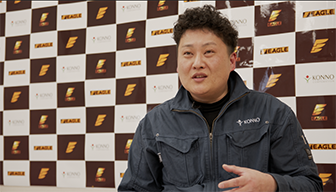
——では、実際に受講生としてスクールに参加した目黒さんにお聞きします。実際にはどのような方法で現場改善を進めていったのですか?
目黒さん まず、工場全体の流れを把握するため、工場レイアウト図をもとに「ものと情報の流れ図」を作成しました。仕入れた原材料が(工場の)どこから運ばれ、(工場の)どこでどのように加工され、(工場の)どこから製品となって出荷されていくのかを、原材料や仕掛品等の「もの」の流れと、それをとりまくさまざまな「情報」(受注指示、加工指示、発注指示等々)の流れを「見える化」し、社員全員で共有しました。そのうえで、「流れ」が阻害されていると感じる箇所=問題点を調査しました。工場レイアウト図に、問題点を爆発マークでわかりやすく示して、社員全員で共通認識を図りました。
次に、問題点と思われる工程に従事している作業者を集め、細かく問題点を検討し、それをもとに「兆候シート」(兆候=表面的な問題点の背景に潜む解決すべきテーマ)を作成しました。
さらに、全作業のリードタイムを測定し、どの作業にボトルネックがあるのかも調べました。
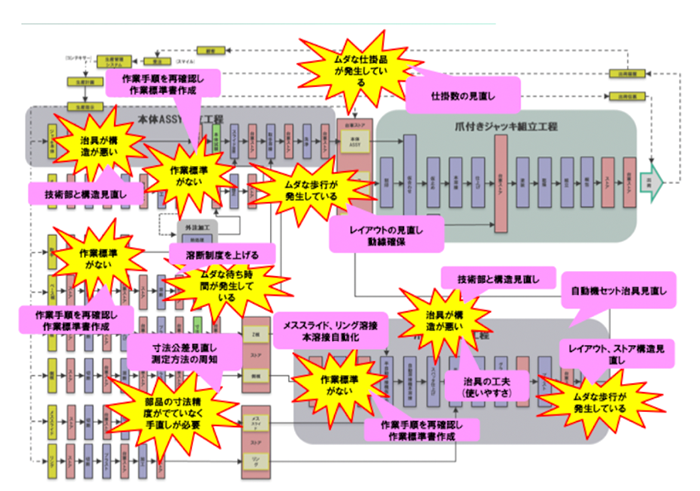
工場内のホワイトボードに重大課題をかき、効果予測を立て、改善効果が高いものからランクづけを行った。すると取組むべき内容が明確化。
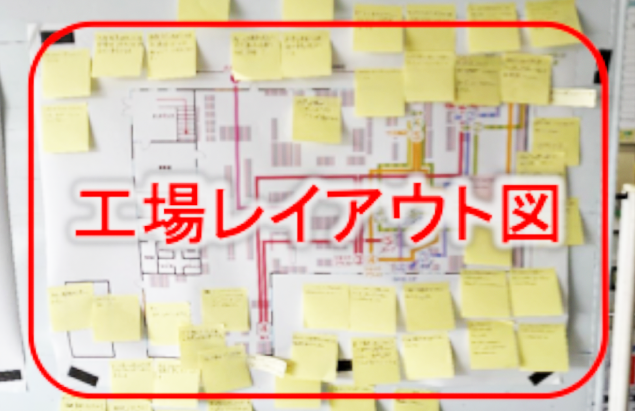
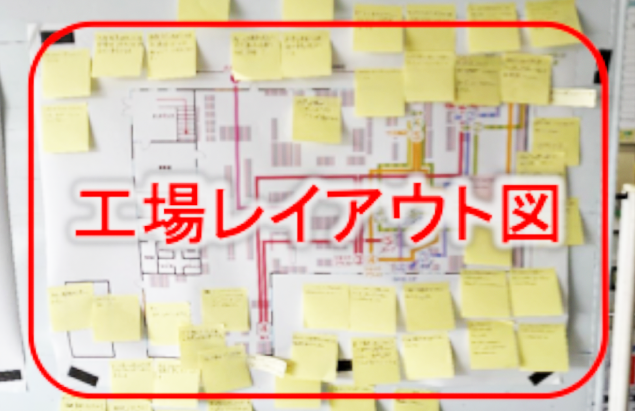
また、改善案に対する効果予測を立て、改善効果が高いものからランクづけを行いました。
各工程の組み立てリードタイムを作り、各作業にかかる時間を洗い出した結果、まずは(ジャッキの)爪の組立工程を見直すことにしました。
——「爪組立工程」の改善は、具体的にどのように進めていったのですか?
目黒さん 最初に「爪組立工程の作業」のリードタイムを作成しました。その結果、「無駄な歩行が多い(改善①)」「治具構造が悪い(改善②)」の2つの問題点が洗い出されました。
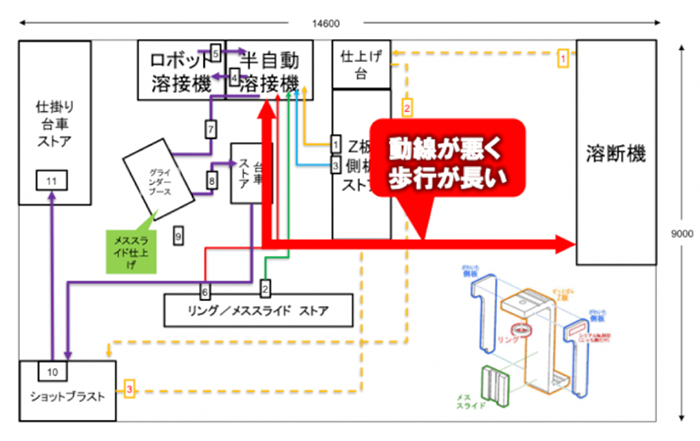
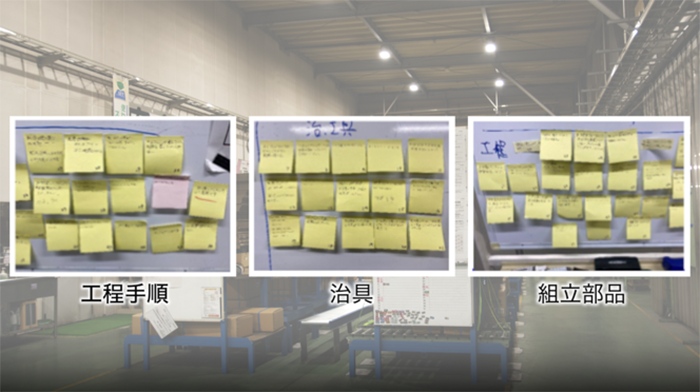
「無駄な歩行が多い(改善①)」については、まず作業者をビデオカメラで一定時間撮影し、作業時間を細かく計測しました。これにより作業者の歩行時間や部品の加工工程で、どこにどの程度の時間がかかっているのかを「見える化」し、無駄の要因となっているレイアウトの変更を行いました。
次に、「治具構造が悪い(改善②)」については、「治具の使いやすさ」を追求するため、本社・技術部の協力を得ながら構造の見直しに取り組みました。従来までは作業者ごとにバラつきが出る治具を3つ使用して一つの作業を行っており、5台の製造時間として20分間かかっていました。
自分一人では改善できないことがたくさんあったので、関係者を集め、東京本社の技術部とも何度もzoomで会議を開きながら、治具構造をみんなで検討しました。工場で作業する現場の人たちの要望を細かく伝え、何度も設計と試作品を繰り返した結果、作業者によるバラつきが出ない治具2つが出来上がり、およそ14分もの時間短縮に成功したのです。
そのほか、溶断品の加工方法も見直し、1個当たりの仕上げに要していた35秒間を0にすることもできました。
——あらためてスクールを受講した率直な感想をお聞かせいただけますか?
目黒さん 最初は専門的な言葉も多く、自分に理解できるのか、正直、途中で不安になったこともありました。けれども、自分が学んだ改善方法を実践していくことで実際に成果が出てくるのを目の当たりにすると、本当に頑張って学んでよかったなと思います。
自分が悪いと思い込んでいた箇所とは違う、意外なところに問題が潜んでいることもあるのですよね。スクールではそういう全体を見てから改善に取組むという指導をしていただき、目の前の問題点しか見ていなかった自分に、全体を俯瞰して物事の流れを見る力が備わった気がしています。
スクールで学んだことを職場のみんなで共有できれば、一人の気づきが社内の気づきとなり、もっと良い改善が出来て、社内全体の生産性を上げていけるのではないかと思っています。
——それでは、福島工場と連携して改善に取り組まれた技術部・菅原さんにもお話をお聞きします。具体的にどのような面で協力されたのでしょうか?
菅原さん 私は、溶接治具の設計製作をサポートしました。従来、使用していた治具は非常に重く、扱いにくいものでした。使う人によって毎回調整が必要なため、手間もかかるうえバラつきが生じてしまう。なんとか改善できないか、福島工場の現場から要望が上がり、期待に応えるべく治具改善に取組みました。
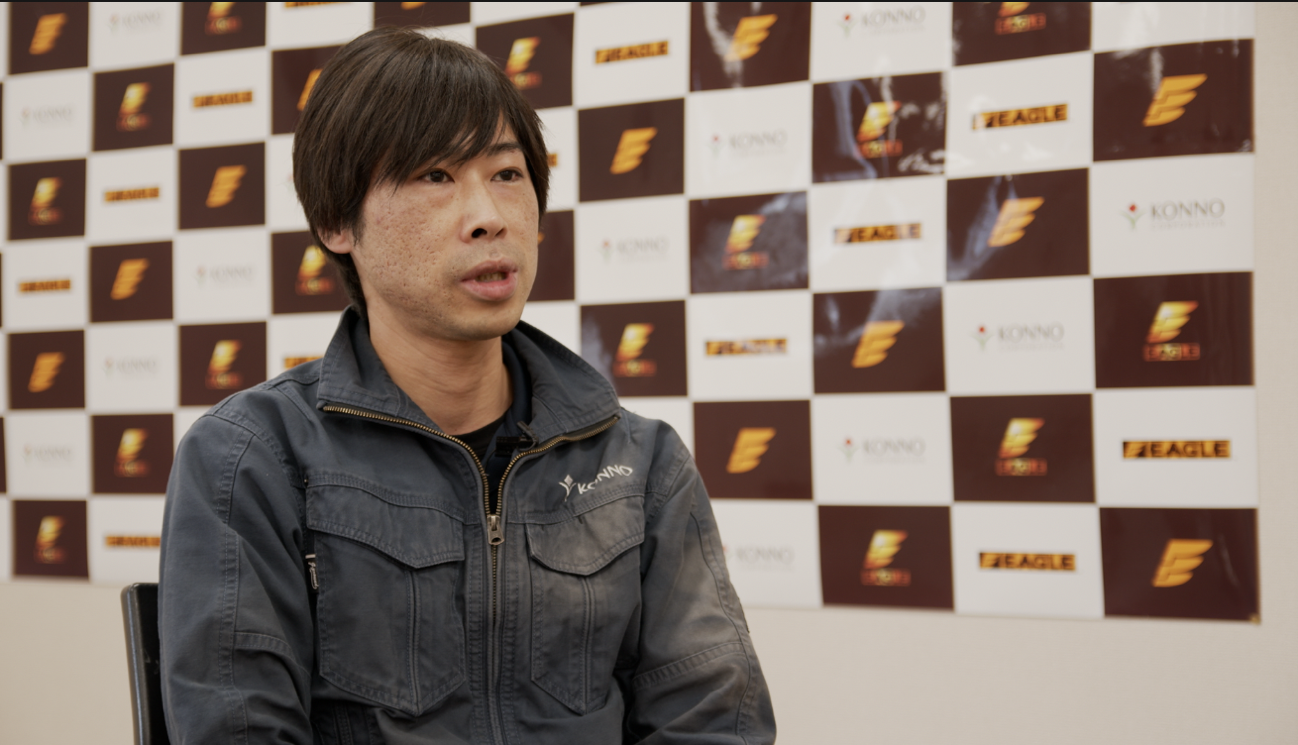
ポイントは2つ。一つは治具の軽量化で、もう一つは2つの工程を1つの工程に集約し、誰が使っても同時間で同じ品質の製品を作ることができるよう設計にすることでした。
こうした改善の取組みはそれ以降もずっと継続して行っており、治具の見直しはもちろん、これまで手作業でやっていた工程を治具化して時間短縮を図っています。
今回の取組み以前は、あまり現場の要望が表立って出されることがありませんでした。が、スクールをきっかけとした今回の取組みを機に、現場の要望があらためて課題として投げかけられ、われわれも全力でサポートしたことで大きな成果につながったのだと感じています。
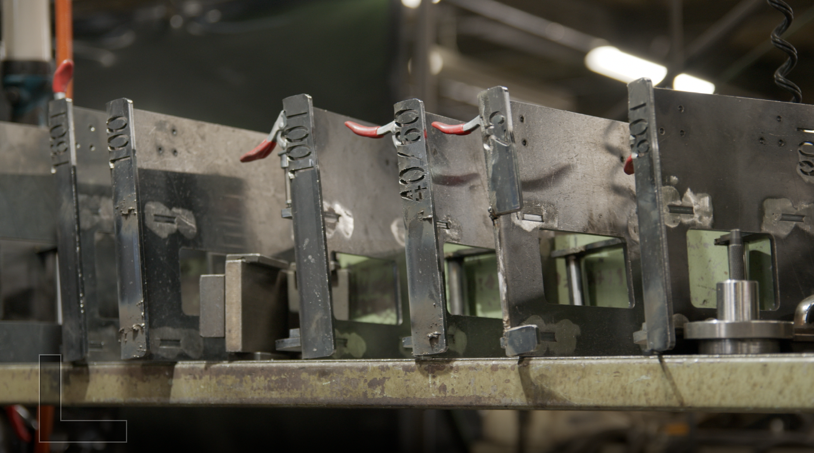
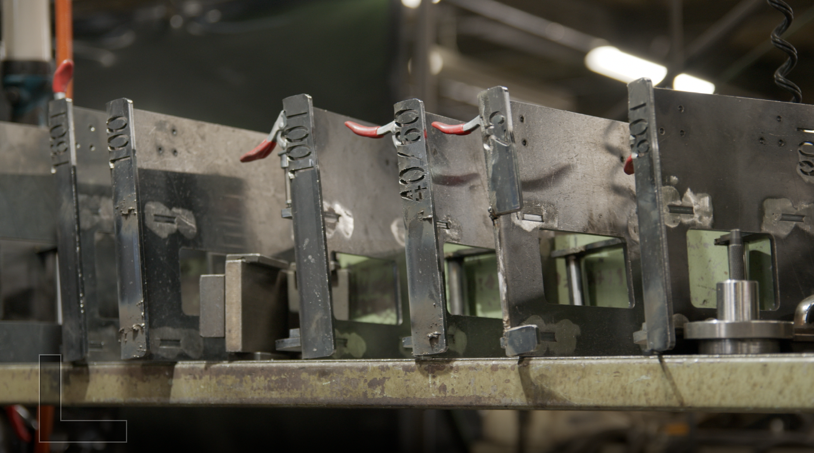
——技術部として今回の取り組みに参加したことで、部署間の連携に変化が見られたようですね?
菅原さん 今までは製造メンバーが、どのように作業しているのかすら、把握できていませんでした。今回の改善を通して、「生産性向上には、まず現状把握が大切」であることを痛感しました。現場がどんなことに困っているのかに耳を傾け、製造メンバーと技術部門が一体となって取組む。この事例によって、今後の問題点を改善していくための良い連携コミュニケーションが生まれたと思います。
先ほども申し上げたとおり、これまでは現場から治具に関する相談の声が技術部に寄せられることがほとんどなかったのですが、その間、現場は現場で工夫していたそうです。今回のように東京と福島で、場所は離れているものの、zoom等の手段を使って一緒に取り組む事ができたことで、今まで顕在化していなかった現場改善の可能性が高まったのではないでしょうか。このような事例が生まれたこと自体、会社にとっても大きな成果だと思っています。
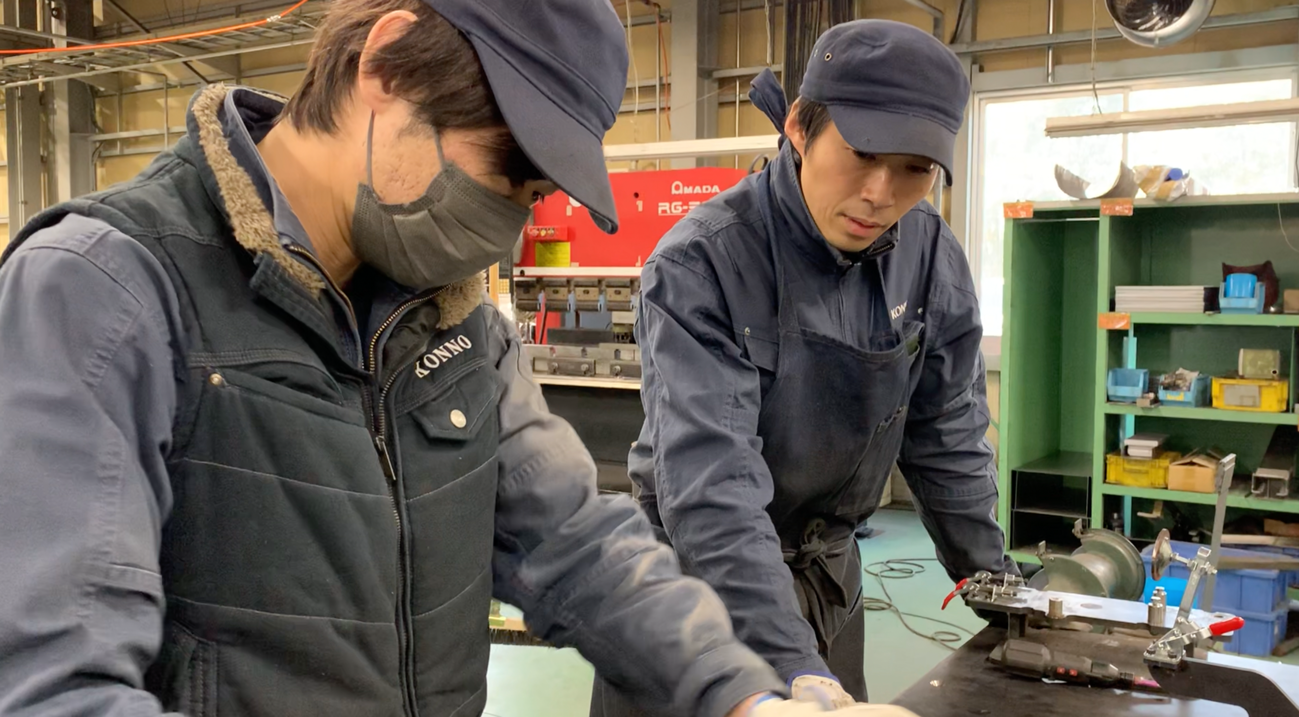
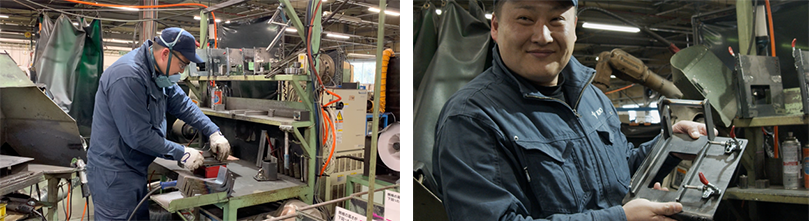
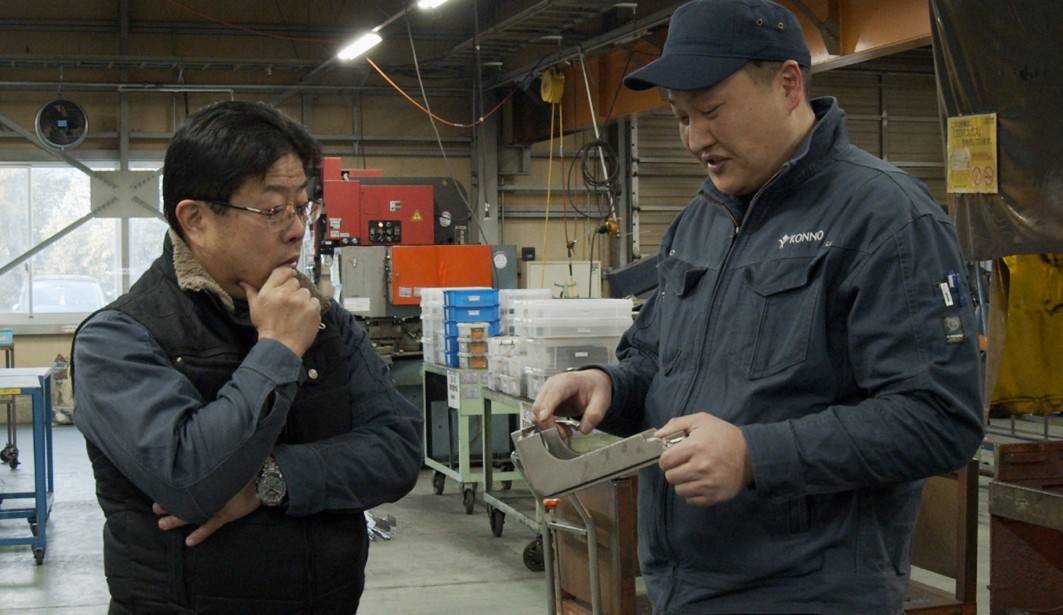
スクールは社員に社長である自分からは直接指導できない様々な“気づき”を与えてくれるといいます。
——最後に今野社長にお聞きします。今回の改善活動についてどのようにお感じですか?
今野社長 今回の改善活動で結果的に生産性は上がりました。現場改善に関する基礎や理論、定石を学ぶことの大切さをあらためて認識させられました。
しかし、一番良かったと思うことは、今野製作所の社員が一丸となって新たなチームワークが生まれたということです。こういう「困りごと」をみんなで解決して、その結果、成果が出る。
今後も当社がモットーとする「力を合わせる力がある」という姿を、レベル高く、実現していきたい。みんなのパスがつながってゴールに向かっていけるーーそうした組織づくりと共に、会社を育てていきたいと思っています。
——スクール受講を検討している、同じものづくりに携わる事業者様に、ひと言お願いできますか?
今野社長 経営者として社員を研修に出すのはコストの増大につながり、大変です。業務も忙しいですし、少人数の職場で1人の人材を3ヶ月間もの間、スクールに通わせるのは正直苦しいです。学ぶ内容も難しいですし、日頃、工場で働いている人間が経営者レベルの視点で生産性を考える講義の内容についていけるのか、という心配も正直ありました。ですが、結果的にみんな想像以上に良い成果を出してくれた。スクールは、社長である自分が直接指導できないさまざまな“気づき”を社員に与えてくれたと感じています。経営者として、ちょっと勇気を持って社員の背中を押してあげる、それだけの価値はあると思います。信じて良かったと思っています。
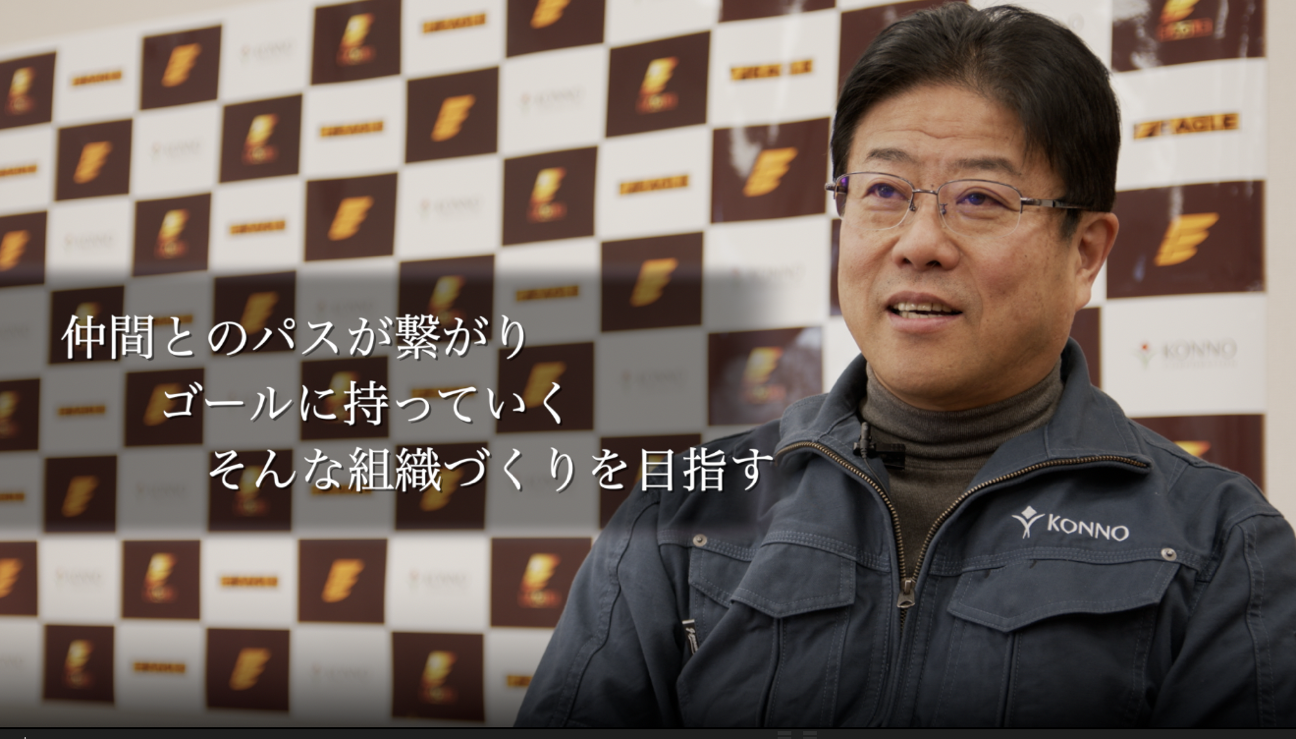
■株式会社今野製作所の会社概要
本社工場 | 東京都足立区扇1-22-4 |
---|---|
代表者 | 代表取締役 今野 浩好 |
設立 | 1969年10月 |
事業内容 |
|
URL | https://www.konno-s.co.jp/ |