東京都ものづくり生産性革新スクール 事例紹介
CASE3 武州工業株式会社
スクール受講をきっかけに個の力を引き出し、
創業時からの改善文化を確実に次代へ伝える
“作業者”から“仕組みを作る側”へ。中核人材の育成こそが持続的な利益を生み出す
創業時からの改善文化を確実に次代へ伝える
“作業者”から“仕組みを作る側”へ。中核人材の育成こそが持続的な利益を生み出す
武州工業 株式会社 | |
![]() |
![]() |
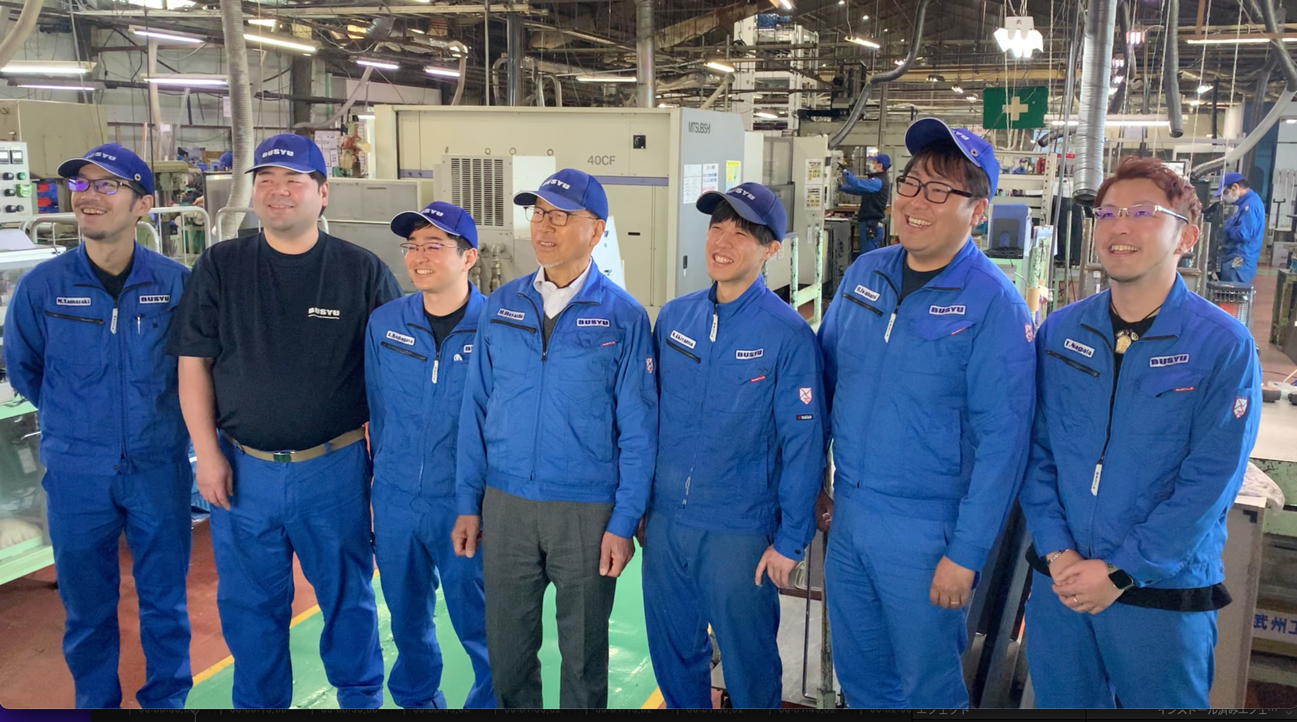
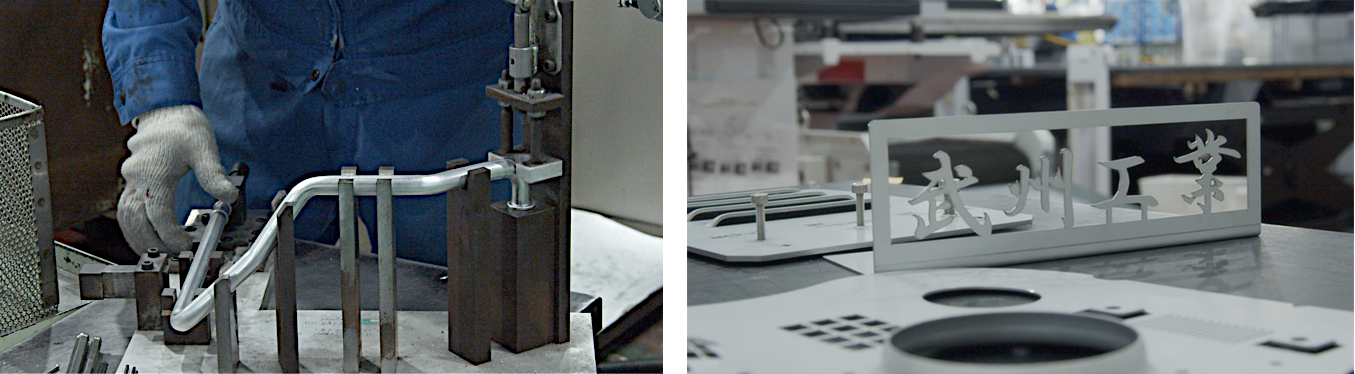
公社では、中小企業の持続的な成長において、新たな付加価値を生み出す「生産性の革新」を担う「中核人材」の育成を目的として、平成28年より「東京都ものづくり生産性革新スクール」(以下、スクール)を開講し、毎年実施している。
昨今、技術革新やデジタル技術の導入が飛躍的に進む一方で、急激な感染症拡大や不穏な世界情勢の影響等により中小企業を取り巻く環境は大きく変化しつつある。それに伴い、企業の中核人材育成の重要性がより一層高まっており、同スクールへ寄せられる期待も大きい。
本稿では、第1期生から同スクールに参加し、計6名のスクール修了生を輩出している武州工業を紹介。創業当初から独自の改善文化をもつ同社では、スクール修了生が現場(工場)をはじめさまざまな部署で活躍し、それぞれの立場で新たな現場改善に取り組んでいる。スクール修了後に見えてきた“学び”や、今現在どのように生かされているのかを聞いた。
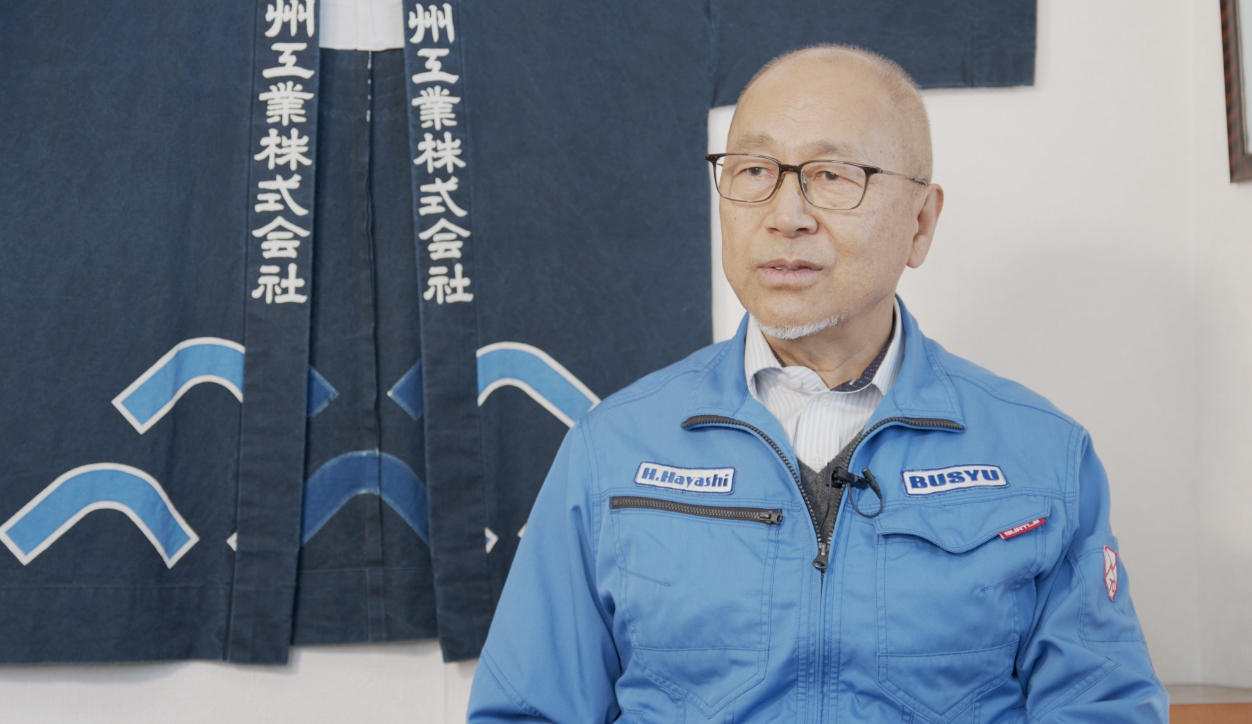
「社員をスクールに受講させることで、同じ目線で物事を考えるメンバーが増えた。人材が育つということは、会社として大きなメリットです。」 林 相談役
——スクールを受講するきっかけは何でしたか?
林相談役 武州工業では長年、独自の「一個流し生産」という方式を取り入れています。この方式は、一人の技術者が材料調達から加工、納期管理まで一貫して行う手法で、これにより当社では品質の高い商品を効率よく生産してきました。が、時代と共に、この仕組みを作った人たちがいなくなり、新しい世代の人たちへ、いかに改善手法を継承していくかが懸念材料となっていました。そんな中、公社でスクールを実施することを知り、スクールの趣旨とわが社の目指す方向性が一致したことから、早速、社員に参加してもらうことにしたのです。
技術継承が途切れると生産性は確実に低下すると考えています。業務を「見える化」し、無駄のないマニュアルを作成して、次代へと技術をつなぐ。時代に合わせた改善は会社の未来のためにも避けては通れないと考えています。
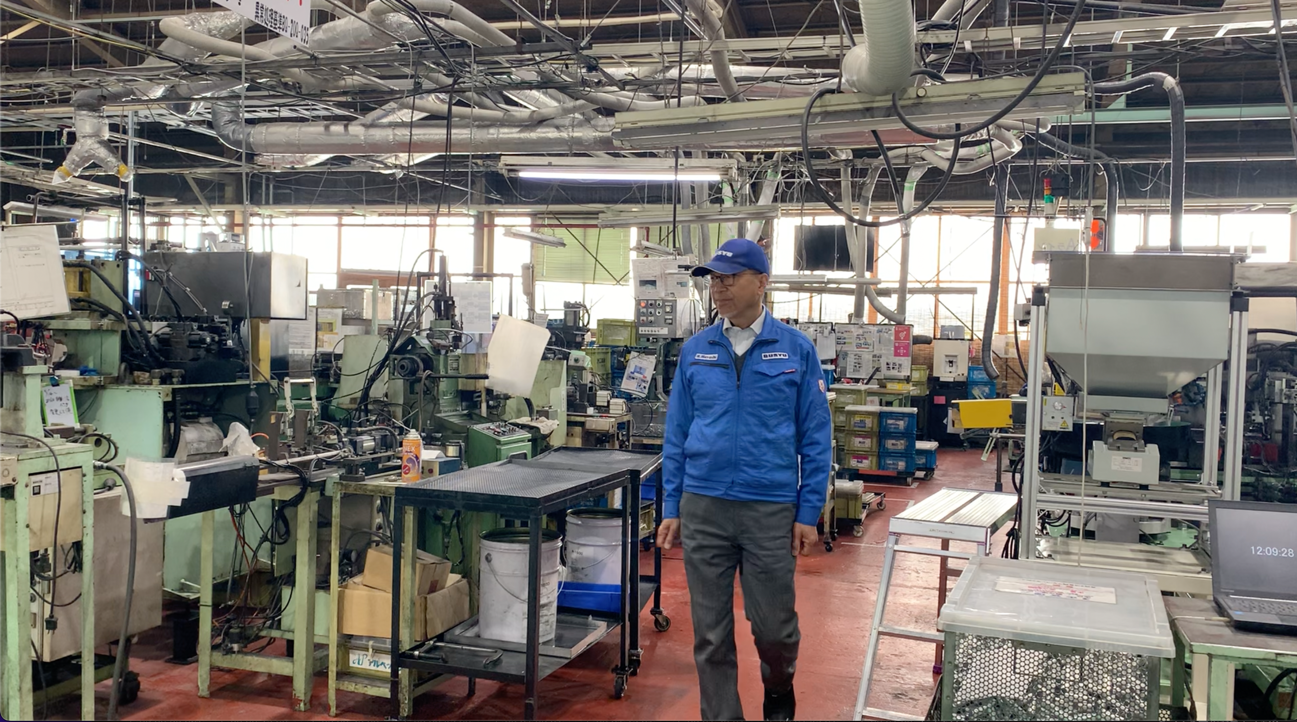
——それでは、第1期生として受講された山崎さんにお聞きします。当時、製造部の班長というお立場でスクールに参加され、そこで学んだことについて教えてください。
山崎さん メインは生産性向上を目的とした現場改善手法ですが、ほかにも社内コミュニケーションの取り方や経理業務など多くのことを学びました。
班長という立場で様々な製品づくりに携わっていましたが、製品ごとに見れば、業務はあたりまえのように毎日流れていきますし、当時の私は、取り立ててどこかに問題があるようには見えませんでした。
しかし、スクールで「全体の流れ」を俯瞰して見ることを学び、目線を変えて眺めてみると、工場の動線や作業工程に対して、「果たしてこれでいいのか……?」と感じるような様々な疑問が生まれてきたのです。例えば、それまで離れた場所で行っていた複数の作業も、業務的に連動するのであれば同じ場所で加工した方が効率が良いのでは?という感じです。そうすることで時間も人も削減でき、機械の稼働率も上がりますよね。ちょっとした事かもしれませんが、積み重ねていけば生産性が大きくアップします。
——スクールで学んだことは周りの社員にも伝えたりされたのですか?
山崎さん 機会があれば伝える努力はしていたのですが、当時は私しか学んでいなかったものですから、思うようにいかず、(林相談役には)毎年誰かしら参加させてほしいと頼みました。最近は、スクール修了生もふえてきて、お互い考えていることや学んだことが同じなので、徐々に会話がかみ合ってきた気がします。今は7年かけて計6名の修了生が各部署に配属され、それぞれ独自に現場改善に取り組んでいるので、改善のスピード感というか、発信スピードがとても速くなったと感じています。
山崎さん 機会があれば伝える努力はしていたのですが、当時は私しか学んでいなかったものですから、思うようにいかず、(林相談役には)毎年誰かしら参加させてほしいと頼みました。最近は、スクール修了生もふえてきて、お互い考えていることや学んだことが同じなので、徐々に会話がかみ合ってきた気がします。今は7年かけて計6名の修了生が各部署に配属され、それぞれ独自に現場改善に取り組んでいるので、改善のスピード感というか、発信スピードがとても速くなったと感じています。
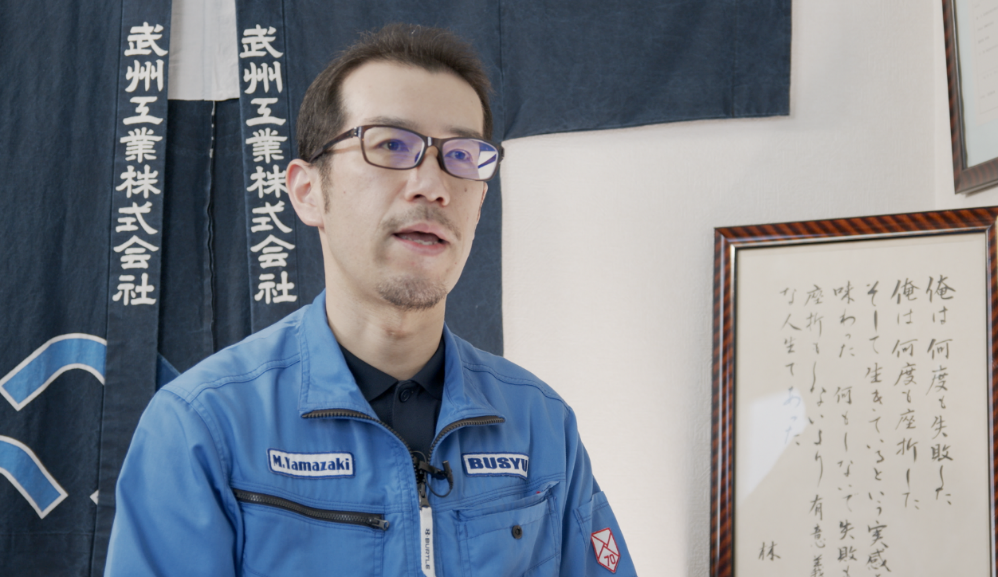
——今はどのようなお仕事をされていて、スクールで学んだことはどのように活かされていますか?
山崎さん 今は新規事業創出グループという部署で、主にAI検査機の開発やシステム開発など、社内向けの設備開発を担当しています。こうした検査機を導入することによって現場作業者の手が空くことになりますが、その分、今度は「モノを考える」仕事に従事してもらって、現場の効率アップと作業者の能力アップ、新しい仕事の獲得もあわせて実現していくことを目指しています。
社内向けのシステムを開発する際にも、当然、現場の知識が必要となるので、スクールで学んだ改善手法を自然と活用しています。
——山崎さんに続いて受講されたのが、当時同じく製造部に所属していた岩浪さんでした。スクールで学んだことで、ご自身の考え方や行動に変化はありましたか?
岩浪さん スクールを受講したことで、今まであたりまえにやっていたことが必ずしも正解ではないということ、全体的に生産性を向上させるには、人やモノの流れを意識しなければならない、ということに気づくことができました。
スクール修了後は、目についた場所を部分的に変えていくのではなく、作業の前工程から後工程までの全工程を考えてラインを構築することを意識しました。結果的に生産性を上げることに成功し、現状の生産体制の仕組みを見える化したことで、必要な設備投資につなげることもできましたね。
(現場は)「変えたい」と思っても簡単に変えられるものではありません。でも、ラインを流してみないことには生産性の良し悪しはわかりません。スクールで学んだ「良い設計の良い流れ」を念頭に置きながら、どうすれば生産性が上がるのか考え続ける——そうした考えが持てる事自体が重要なのではないでしょうか。
今はプレイングマネージャーという立場で、会社全体の動きに関わる目線で仕事をしています。生産性はもちろんですが、人の流れや適材適所の人員配置、班の雰囲気を良くするために、どう人を誘導すべきか、等を考えるうえでスクールで学んだ手法を活用しています。
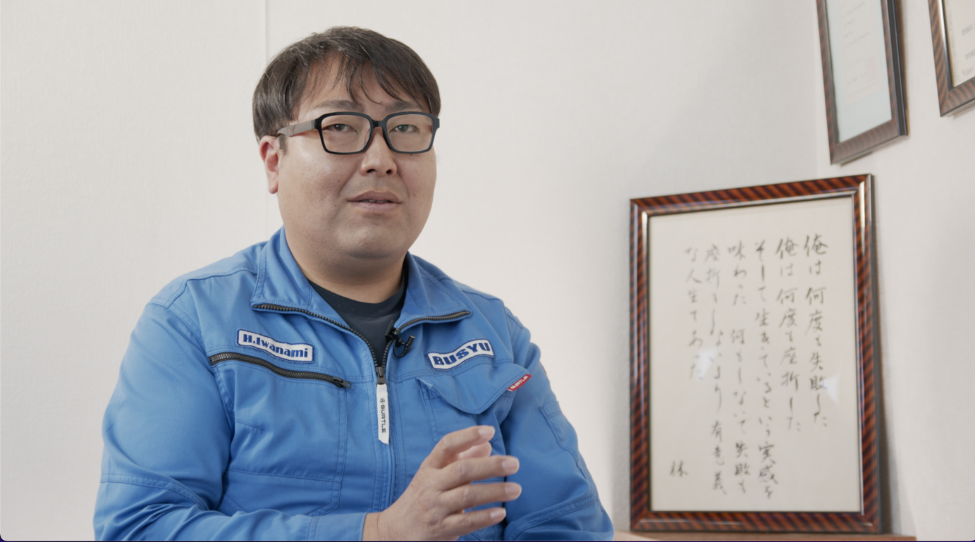
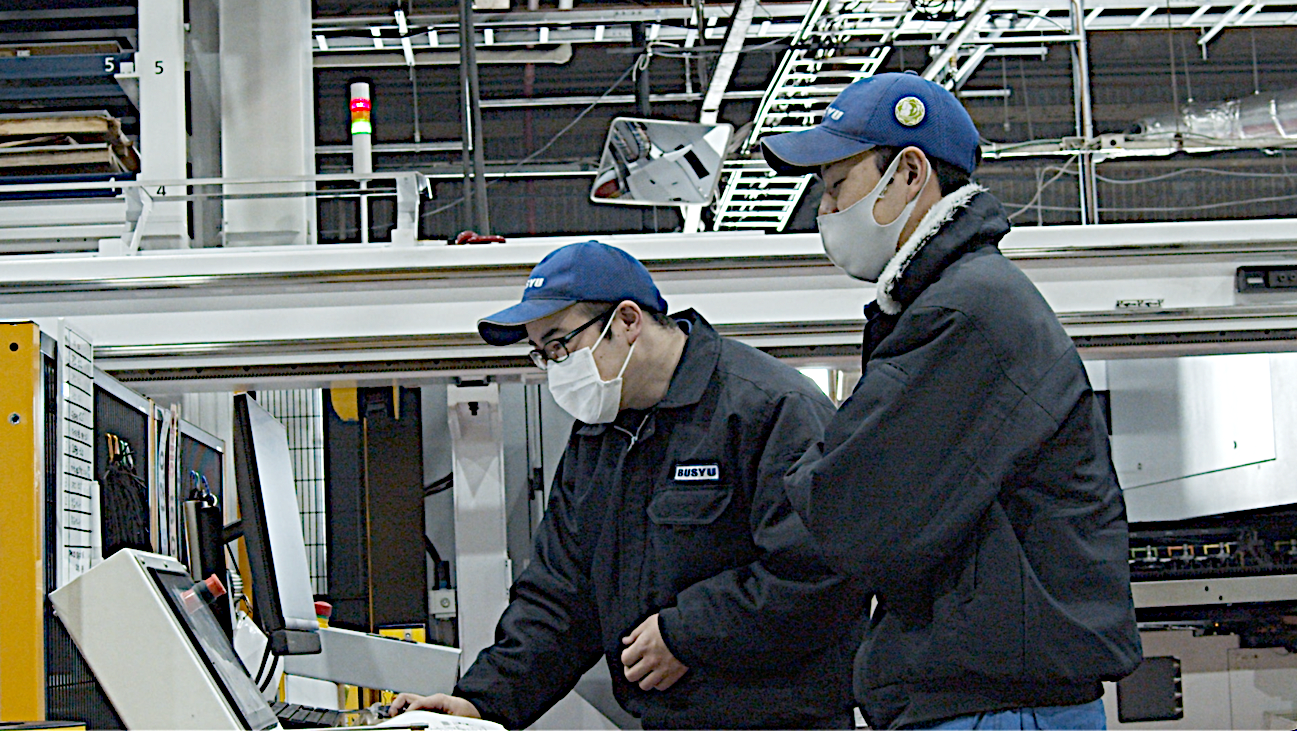
阿利さん 私は、半導体関連部品の組み立て作業に従事しています。スクールで学んだことをきっかけに、人によって異なる作業手順を統一することで、全体の流れと、作業スピードをアップさせることに気づき、改善に取り組みました。
モノを作るとき、ある人はパーツを左から取って、右に流していくのに対し、右から取って左に流す人もいます。些細なことですが、1日何十回も繰り返し行っていると、部品の取り方一つで流れが格段に悪くなり、スピードが落ちてしまうのです。
また、スクールでは違う業種の人たちと一緒に学んだので、別の考えをもった人たちと接する機会がもてたことで、新しい考え方にふれることができ、自分自身とても新鮮でした。
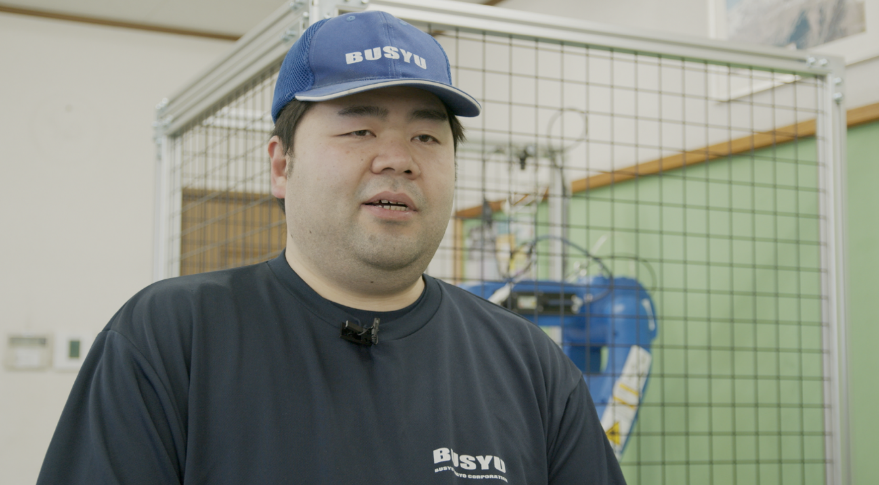
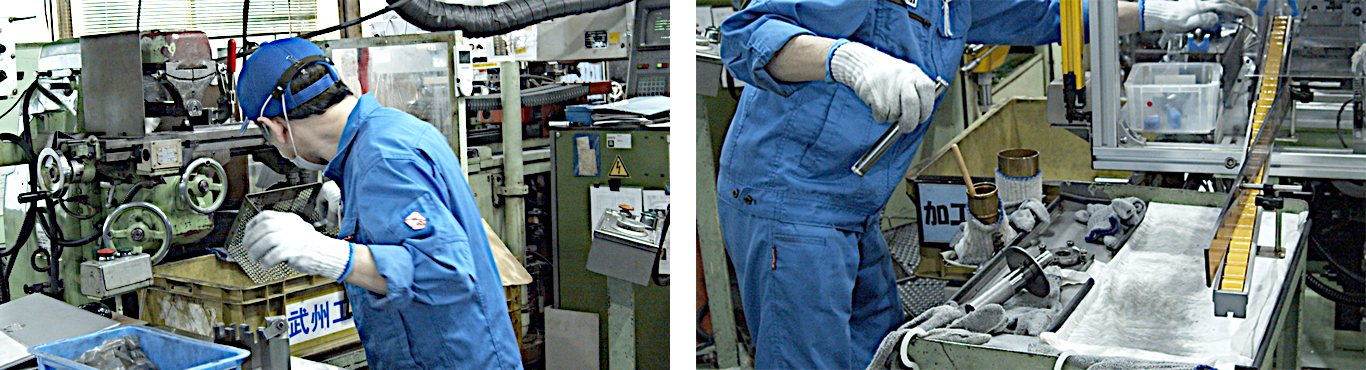
——続いて、間接部門から初のスクール受講生として参加された長田さんにお聞きします。スクールの受講前と受講後とでご自身で変化を感じられましたか?
長田さん 何より、お金の目線で物事を捉え、会社全体の利益を考えるようになりました。
受講前は、新たな学びを得るたびに、今まで意識した事のない考え方ばかりで理解するのに時間がかかりましたが、今思えば身になる授業ばかりだったと感じています。
他のメンバーは皆、現場出身者でしたが、私だけ間接部門出身ということで、現場の外からの目線でどのような改善に取り組めるか、が課題でした。
極端な話、生産性を考えずに働いても、仕事は普通に回るんですよね。ただ、やはり生産性を考えて働かないと効率は悪いままです……。働いても働いても成果に結びつかない、なんてもったいないので、一人一人が生産性を意識する事がとても大切だと思っています。
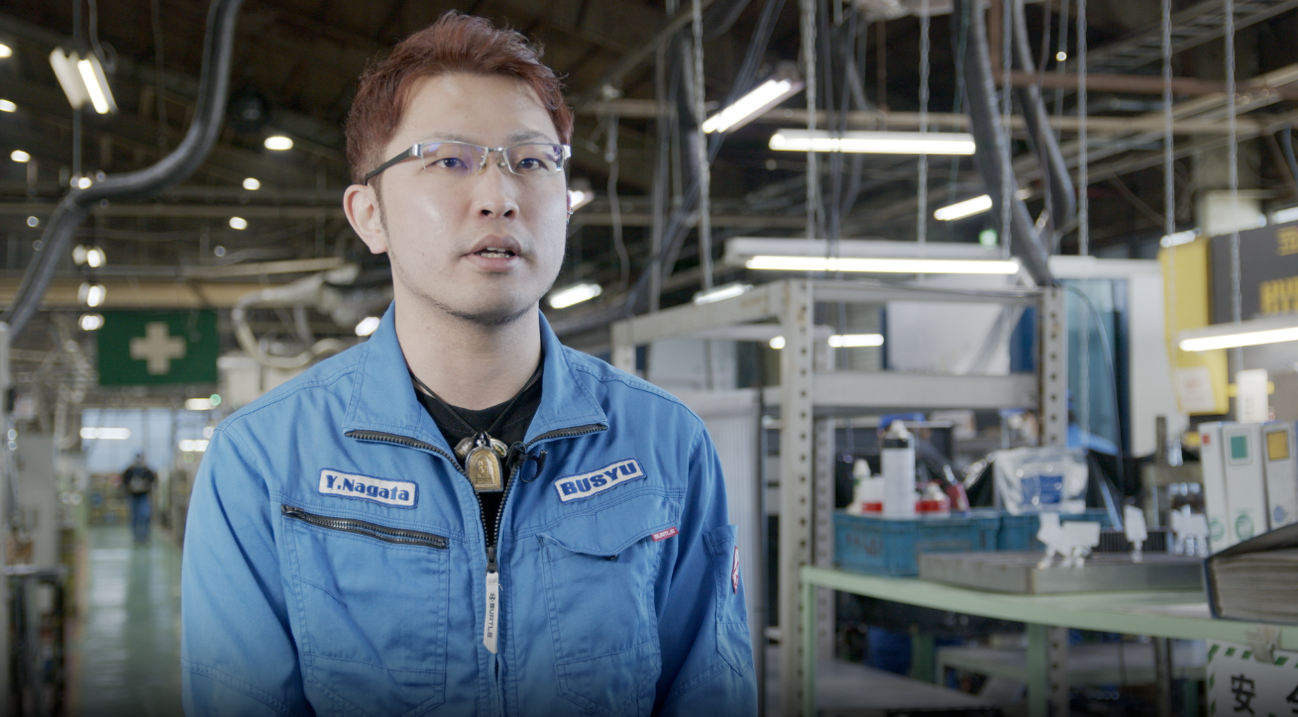
——最後に、お2人同時にスクールを受講された小長谷さんと秋山さんにお聞きします。たくさんの先輩修了生がいるなかで、お2人が学んだこと、2人だから感じることができたことなどを教えてください。
小長谷さん お互いの発想が偏らないという点で、物事を違う視点から考えることができた点が最大のメリットでした。私は今まで人に頼ることが苦手で、仕事もすぐ一人で抱え込みがちでしたが、一緒に受講したことで信頼できるパートナーができたと思っています。あたりまえですが、仕事は一人ではできません。部下を信用して「任せる」大切さを学び、いい意味で「人に任せる事ができる人間になった」ような気がします。
秋山さん 当社は多くのスクール修了生がいるので、先人の皆さんに事前に知識をいただく機会が多く、難しい問題も比較的早く理解できたと思います。2人で、「これはこういう事だよね」と話し合ったり、講義で学んだことを自分たちの現場と重ね合わせながら予習・復習もできました。2人で受講したことで一層、高め合うことができたのではないかと思います。
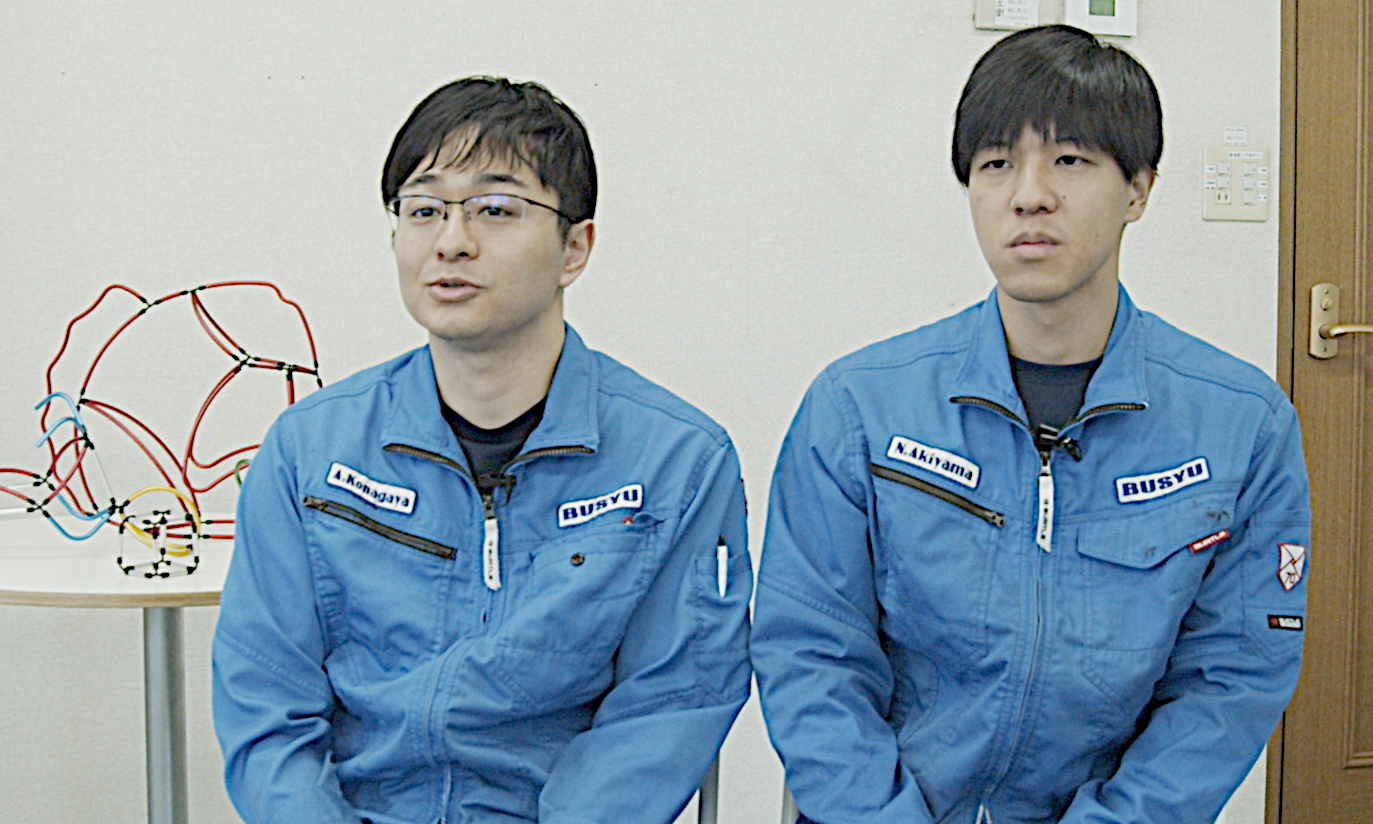
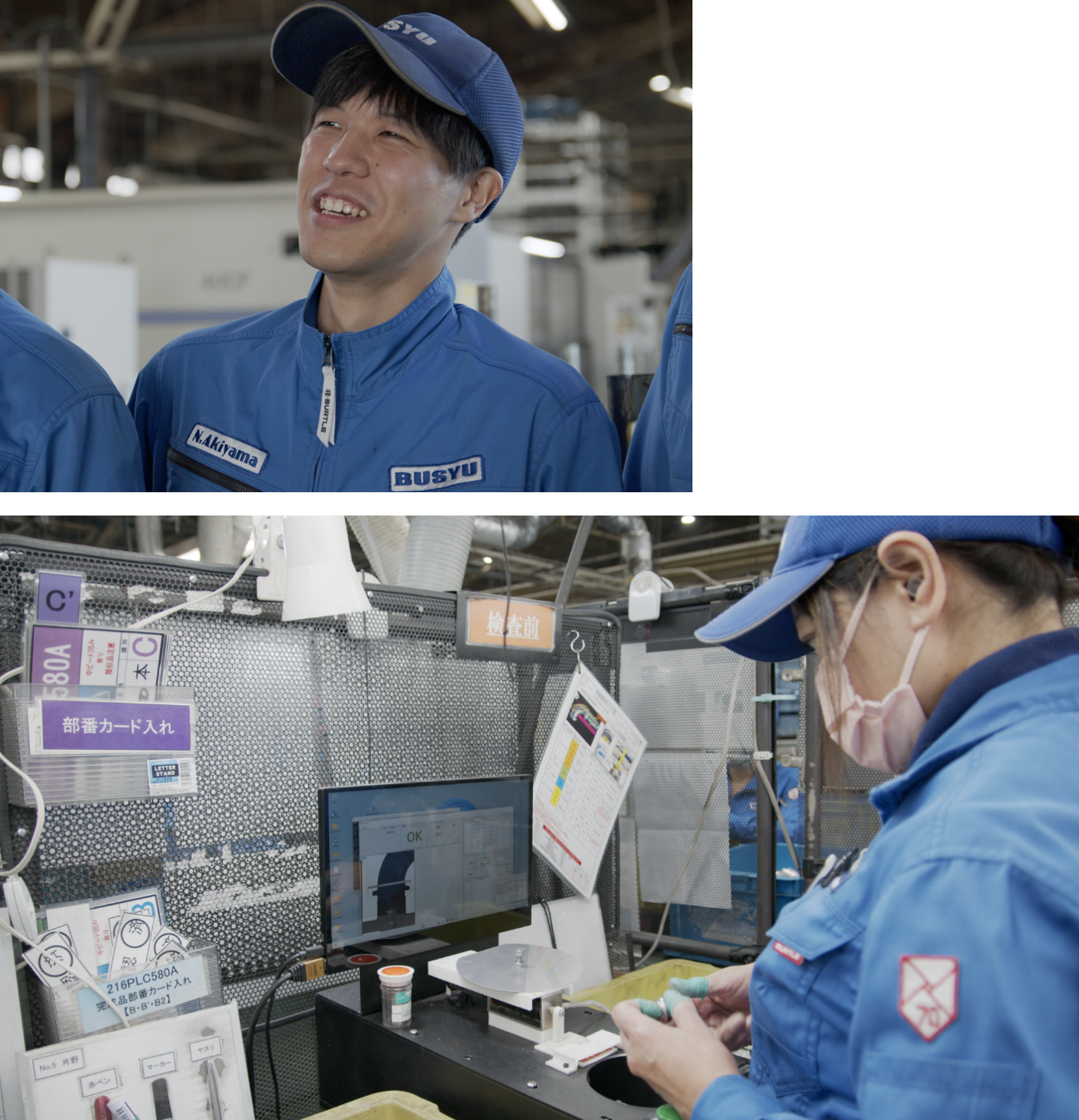
——スクールを修了した皆さんが、いろいろな部署に配属され、共通認識のもと異なるアプローチで改善活動を展開しています。この点を「チームものづくり」武州工業としての強みの一つに挙げる修了生もいらっしゃいました。
最後に林相談役からみた今の修了生たちに対する想い、そして武州工業が目指す今後の展望についてお聞かせいただけますか?
林相談役 みんなに共通して言えるのは、今までは作られた仕組みの中で作業をする立場だった人たちが、スクールを受講してからは、仕組みを作る側に回ってきたということでしょうか。スクールでも学ぶ「良い設計の良い流れ」の考え方にあるとおり、“良い設計”——つまり仕事の仕組みを考えるということがとても大事で、そこから考えることができる人たちがふえてきた気がします。
また、スクールを受講したことによって、一人一人のもっている力がより発揮されやすくなったと感じています。自分の意見をもちながら周囲を巻き込んでいけるチームワークが育ってきました。当社の理念である「モノづくりで世の中の課題にチャレンジし続ける会社」。その実践を意識できる中核人材が確実に育っているのではないでしょうか。
武州工業では今後、DX認定を目指していきます。テーマは「武州テック」です。武州テックとは、我々が自社のために考え、構築してきた仕組み・設備・ノウハウを、世のために共有する——外に出していく取組みを言います。
今、当社と同じような課題に直面している中小企業のためのプログラムをまとめているところです。いつまでも世の中の課題にチャレンジできる会社でありたい。それが武州工業の使命だと考えています。
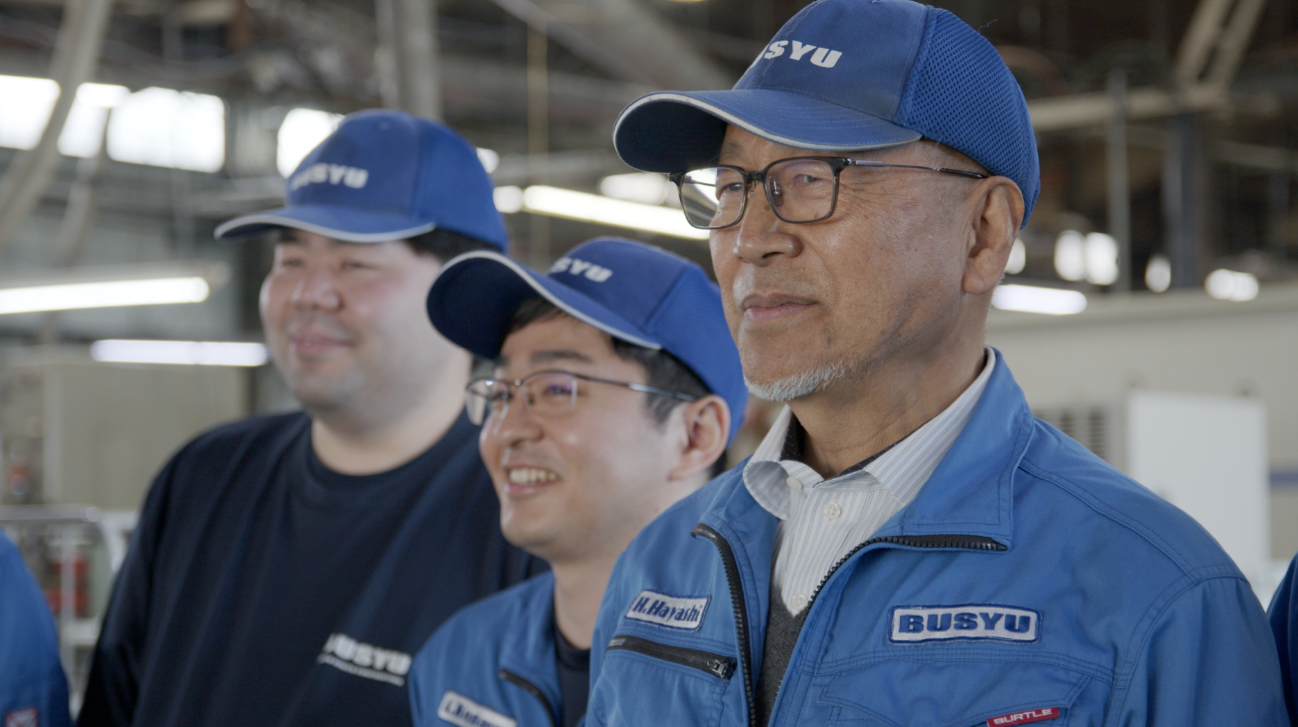
■武州工業株式会社の会社概要
本社工場 | 東京都青梅市末広町1-2-3 |
---|---|
代表者 | 代表取締役社長 林 英徳 |
設立 | 1951年 |
事業内容 |
|
URL | https://www.busyu.co.jp/ |